We are continuously working to use more sustainable equipment and become more energy-efficient – from the pencil to the data center, from the screw to the machine, and from the office to the production halls and warehouse. To achieve this, we regularly review and optimize our procedures and processes.
Worlée-Chemie is continuously working to reduce electricity consumption. In recent years, we have been able to increase our efficiency by more than 20 percent at Worlée-Chemie alone—our energy management has been ISO 50001 certified since 2013. Let’s take a closer look at the areas where changes have been made at Worlée-Chemie:
- Overhaul of all compressed air systems with the aim of saving energy
- Heat recovery in ventilation systems and from compressors
- Thermal utilization of waste
- Use of thermal imaging cameras to detect insulation weaknesses
- High-speed doors
- Process heat sourced from a biogas plant
- Reduction/replacement of conventional lamps with LED lights, maintaining the same level of brightness
- Optimized process control
- State-of-the-art motor technology
- Consideration of energy efficiency aspects in all purchases, new constructions, and renovations
- Sophisticated consumption monitoring
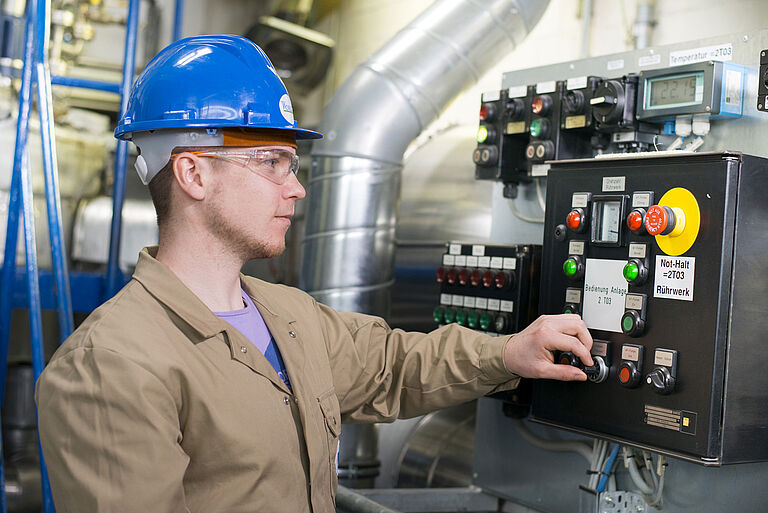
In recent years, Worlée has built a new administration and technical center at its headquarters in Hamburg. It meets the KfW-75 standard, consuming only 75 percent of the primary energy of a reference building. An administrative building from the 1970s has already undergone energy-efficient renovation, featuring LED technology, double-glazed windows, an insulated facade, and a photovoltaic system with a heat pump that covers the entire heating requirement of the building. In 2024, the main building will be upgraded to a KfW-40 standard and renovated, also featuring facade insulation, double-glazed windows, and LED lighting with intelligent control. A new photovoltaic system on the roof is expected to generate around 250 kWp of power. We plan to build additional photovoltaic systems and implement other energy-saving measures.
Through our extensive commitment to sustainable energy efficiency, we are also an Environmental Partner of the city of Hamburg, which we are very proud of. Furthermore, we are involved in the Energy Efficiency Networks initiative for the food industry, initiated and supported by the Federal Ministry for Economic Affairs and Energy (BMWi) and the Federal Ministry for the Environment, Nature Conservation, and Nuclear Safety (BMU).
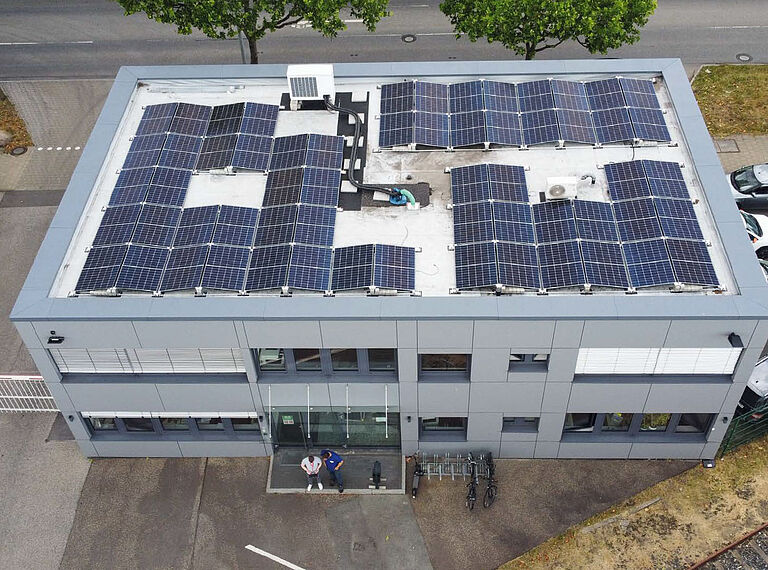
In large factories, waste is inevitably generated, but what matters most is how the valuable materials are handled. Can they be processed and recycled, or disposed of in an environmentally responsible manner? At Worlée, we always choose the most sustainable path.
Since August 1, 2017, businesses have been required to manage and document waste, including sorting and accounting. For us, waste reduction and responsible handling of valuable materials are of the highest priority. Therefore, we separate waste by type and have it processed in local recycling plants or disposed of in an environmentally friendly manner.
For example, this is how we handle waste products at our chemical plant in Lauenburg:
- Solvent recovery for reuse
- Multiple use of sodium hydroxide (cleaning agent)
- Replacement of metal sample containers with paper cups
- Thermal recovery of liquid waste in our afterburning plant
- Continuous monitoring of quantities and costs through our economic management system
With our waste management system, we aim to contribute to conserving resources and reducing climate-damaging greenhouse gas emissions.
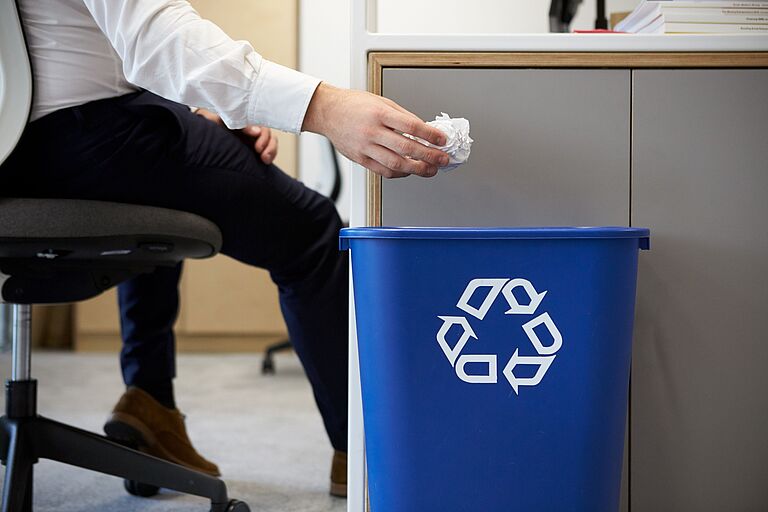
Where chemical substances are handled, safety management plays a crucial role. Our chemical division operates a certified environmental management system (ISO 14001), occupational safety management system (ISO 45001), and safety management according to Section 12 of the Federal Immission Control Act (BlmSchV), which goes well beyond the legally required standards.
In addition to essential safety measures such as floor encapsulation and the avoidance of industrial wastewater, we place particular emphasis on proactive measures at our chemical plant in Lauenburg. Our employees undergo regular training to conduct comprehensive risk assessments in all areas of production. Together, we analyze all potential risks in advance that could lead to accidents. This is the safest way to prevent accidents from occurring in the first place.
What to do in case of disturbances at the Lauenburg site?
Our comprehensive safety management system ensures that the risk of an incident affecting the environment is minimized. However, if an incident does occur, an alarm and emergency plan is activated, which regulates the further actions within the plant site and in the surrounding area.
Download "Informationen für die Öffentlichkeit" (only in German)
The last inspection according to Section 16 of the Major Accident Ordinance was conducted on Aprli 1, 2025.
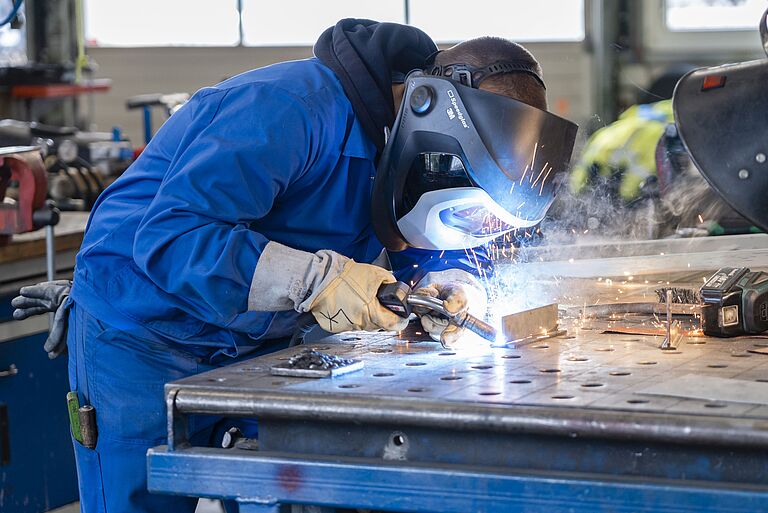